В гостях у сказки. На базе Renault F1 в Энстоуне...
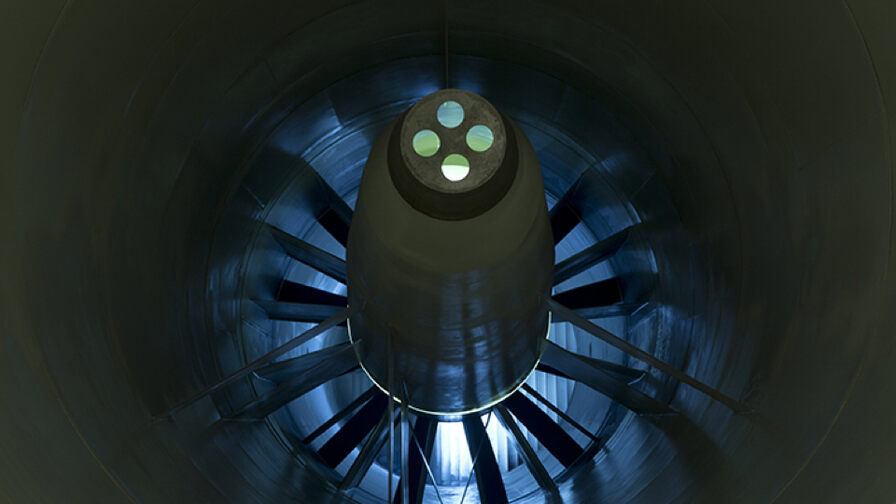
Пока идут предсезонные тесты в Формуле 1, мы вместе с Николя Карпентье совершим прогулку по святая святых команды из Энстоуна, заглянем в отдел проектирования шасси и даже побываем в сердце любого конструкторского бюро – в аэродинамической трубе. Поехали...
Проектирование современной машины Формулы 1 – дело исключительной сложности, сопряженное с огромным количеством факторов и нюансов, которые необходимо принимать во внимание, чтобы слово не расходилось с делом. Слово здесь – это компьютерная модель и чертежи, а дело – реальное шасси, которое однажды появится на трассе.
Один только отдел проектирования шасси в Renault F1 насчитывает более 70 человек, которые разбиты на несколько групп, включая департамент разработки трансмиссии, отдел механических конструкций, отдел анализа нагрузок на элементы и группу контроля производительности финальной продукции.
Огромный офис открытого типа наполнен рабочими столами с перегородками для лучшего взаимодействия между сотрудниками и отделениями.
На проектирование всех 14,500 компонентов готового шасси уходит 150,000 человеко-часов, а на выходе получается 19,000 компьютерных чертежей в виде файлов системы автоматизированного проектирования. При этом работа над элементами нового шасси начинается примерно за полтора года до старта сезона.
Каждый год Международная автомобильная федерация обновляет свод законов и требований к дизайну шасси, и все эти материалы тщательно изучаются в отделе проектирования перед тем, как приступить к работе над новой моделью.
Все сотрудники отдела проектирования в Renault F1 подчиняются главному конструктору Мартину Толлидею и его заместителю Симону Виррилу, которые держат ответ перед техническим директором департамента шасси Ником Честером.
Дизайнер Мария Бертель, работающая в Энстоуне с 2014 года, пролила свет на то, как организованы процессы в отделе проектирования.
«Наш департамент разделен на несколько участков, которые отвечают за коробку передач, механические компоненты, подвеску и композитные материалы. Всего нас здесь более 70 человек, – рассказала Мария. – Также у нас есть очень важный отдел анализа нагрузок на элементы, с которым мы очень тесно работаем. Все композитные материалы первым делом направляются на анализ нагрузок, и только после этого мы финализируем их конструкцию».
От замысла к реализации
Формула 1 работает в бесконечном цикле, и когда один сезон начинается, на базе в Энстоуне уже готовы все базовые чертежи для шасси следующего года.
Однако очень трудно выдерживать баланс между доводкой машины нынешнего сезона и проектированием следующей.
Что касается разработки дизайна элементов шасси, то на некоторые из них уходит всего пара дней, а на другие – к примеру, такие сложные, как корпус коробки передач, – до нескольких месяцев. Скорость и точность – наше всё в Формуле 1.
Рабочие процессы в отделе композитных материалов целиком и полностью подчинены департаменту аэродинамики. Они получают от аэродинамистов макеты деталей, проверенные в аэродинамической трубе, и запускают их в производство.
«Всё завязано на требования технического регламента FIA к деталям шасси, – продолжила Мария. – Когда специалисты по аэродинамике остаются удовлетворены своими разработками, они передают их нам, и мы уже пытаемся произвести детали, которые и будут установлены на реальное шасси на трассе.
Но этот процесс не так прост, как кажется, особенно когда дело касается переднего антикрыла и боковых дефлекторов. Эти элементы крайне сложны в производстве. В этом году конструкция переднего крыла» будет упрощена, но, как мне кажется, боковые дефлекторы добавят нам головной боли.
Знаете, иногда мы получаем опытные модели от аэродинамистов, смотрим на них и восклицаем: «Да как такое вообще можно произвести на свет?!» У нас ведь нет в запасе бесконечного времени, обычно от нас требуют довольно оперативного производства деталей.
Конечно, любую форму можно воспроизвести, но сложность состоит в изготовлении шаблона для чрезвычайно мелких и сложных деталей. Нам приходится делить такие конструкции на составляющие и выпекать их отдельно.
Кроме того, иногда детали бывают настолько малыми по размеру, что им требуется подпорка – примеры таких компонентов вы можете видеть на боковых дефлекторах».
Поверхность и структура
Мария пояснила сложность производства некоторых компонентов шасси на примере носового обтекателя, с которым ей частенько приходится работать и который требует аэродинамической и структурной эффективности.
«Носовой обтекатель – особенная составляющая шасси, ведь он должен быть совершенным в плане аэродинамики, – заметила Мария. – Есть внешняя оболочка – скорлупа, – а есть внутренняя, включающая в себя структуру безопасности.
Эта структура может иметь самую разную форму и разное покрытие. Эффективность обтекателя на тестах зависит от способа ламинирования его поверхности, поскольку нос шасси должен поглощать фиксированное количество энергии в течение определенного времени после столкновения. Это тоже требование FIA.
Расположение слоев облицовки играет существенную роль в плане эффективности обтекателя в целом. При ламинировании деталей мы создаем целую специальную книгу, в которой указаны слои один за другим. К примеру, для боковых структур безопасности FIA четко регламентирует процесс нанесения слоев.
Помимо аэродинамических характеристик и требований по безопасности носовой обтекатель должен отвечать определенным нормам жесткости на кручение, поскольку к нему крепится переднее антикрыло, и в этой области FIA применяет серьезные ограничения на отклонение рабочих плоскостей под нагрузкой».
Трудности роста
В рамках плана по возвращению Renault на вершину Формулы 1 в Энстоуне идет постоянное расширение мощностей и численности персонала во всех без исключений направлениях. Однако привлечение новых сотрудников в отдел проектирования не всегда является легкой задачей.
«В плане коммуникации у нас нет никаких проблем, поскольку офис полностью открыт, – продолжила Мария. – Проблемы большого офиса кроются в том, что наши задачи становятся всё мельче и мельче.
В небольшой компании я бы полностью занималась анализом деталей под нагрузкой, тогда как здесь мои функции ограничиваются составлением чертежей и передачей их в отдел анализа.
К счастью, в Renault мы каждый раз работаем с разными деталями, а не делаем одну и ту же работу постоянно.
После выполнения своей части работы я точно знаю, где сейчас шаблоны и на какой они стадии находятся. Я знаю, с кем нужно связываться по тем или иным вопросам, почему отверстие в этой детали расположено именно здесь, а не на 5 мм выше или ниже. В то же время при переходе к новым компонентам мне приходится изучать регламент, поднимать архивы и смотреть, что мы делали в прошлом году, какие слои использовали и так далее.
В данный момент я работаю над торсионной балкой, которая служит для поддержки определенного дорожного просвета. В FIA жестко контролируют клиренс шасси.
К тому же, это очень интересная деталь, ее интересно проектировать, поскольку ее дизайн завязан не только на аэродинамике, но и в большей степени на механике».
Аэродинамическая труба – сердце базы
Ну а теперь мы ненадолго заглянем в отдел аэродинамики, ведь аэродинамика – это самая суть Формулы 1. И первую скрипку здесь, безусловно, играет маэстро аэродинамическая труба.
Оборудование для продувки деталей впервые появилось в Энстоуне в далеком 1998 году и сейчас занимает 2,674 квадратных метра площади.
В 2014 году FIA ограничила работу команд Ф1 в аэродинамической трубе 520-ю запусками в течение разрешенного 8-недельного периода, что составляет примерно 65 запусков в неделю. При этом федерация тщательно следит за выполнением регламента – в каждом помещении установлены специальные камеры, записи с которых предоставляются в руководящий орган по требованию.
На прокатной ленте трубы размещается тестируемая модель шасси масштабом 60% от реальной, а воздух направляется на нее с установленной FIA максимальной скоростью 50 м/с или 180 км/ч.
Все аэродинамические плоскости, появляющиеся на современных машинах Ф1, так или иначе проходят обдувку в трубе. При этом оборудование позволяет проводить тесты по всем трем осям, плюс проводится анализ дорожного просвета, прижимной силы, выхлопной системы и деформации шин.
Главным помощником аэродинамической трубы в нынешней Формуле 1 являются средства вычислительной гидродинамики (CFD). В командах называют их не иначе как виртуальной аэродинамической трубой.
По сути же они представляют собой кластер из суперкомпьютеров, являющийся настоящим произведением искусства и способный симулировать движение воздушного потока вокруг шасси, генерируя при этом свыше 60 терабайт данных в неделю.
«Наша программа проектирования шасси разделена между средствами вычислительной гидродинамики и собственно аэродинамической трубой, – пояснил специалист по аэродинамике Renault F1 Симон Хин. – В отделе аэродинамики работает около ста сотрудников, большинство из которых заняты в работе с трубой, поскольку нам нужно производить и размещать на шасси тестовые детали.
Работа по аэродинамике начинается со средств CFD, и какое-то время идет компьютерное моделирование деталей, исходя из заложенных параметров и характеристик. Когда предварительное моделирование завершено, предполагаемая деталь отправляется на производство шаблона и продувку в трубе для проверки полученных данных симуляции.
При этом в CFD можно делать сразу несколько прогонов, прежде чем переходить к испытаниям на практике. Иногда полученные данные из трубы используются для доработки детали средствами компьютерного моделирования.
Воздушный поток в трубе движется со скоростью 180 км/ч, и 60-процентная модель едет по "беговой дорожке" на такой же скорости. Нам разрешено проводить только 65 запусков трубы в неделю, да и в средствах CFD мы тоже ограничены в отношении количества генерируемых данных.
В Формуле 1 сотрудники часто переходят из команды в команду и рассказывают, что у них было на прошлом месте работы, так что в FIA быстро узнали бы, если кто-то жульничает».
В работе аэродинамического отдела команды Ф1 всё вращается вокруг слова корреляция.
«У нас в распоряжении есть три области исследования: CFD, аэродинамическая труба и трасса. Средства вычислительной гидродинамики с каждым днем модернизируются – еще десять лет назад команды в основном опирались на продувку деталей в аэродинамической трубе. Сегодня же в CFD мы прогоняем в десятки раз больше моделей, чем в трубе.
В идеале мы стремимся к полной синхронизации данных из всех трех областей. И если вы видите, что кто-то на трассе работает с нанесенной на шасси аэродинамической краской, обычно это означает, что в области теоретического моделирования что-то пошло не так и требуется узнать причины этого. К примеру, может происходить срыв потока на переднем антикрыле – средствами CFD это смоделировать очень сложно.
Что касается количества датчиков давления на шасси, то на модели в трубе их обычно от 300 до 400 – главным образом эти миллиметровые сенсоры расположены под днищем. На реальной машине, конечно, столько датчиков не разместишь – у них там много всякой ерунды типа мотора, коробки передач, гонщика… [смеется]
В целом же не так много деталей, которые проходят обкатку на CFD и в трубе, в итоге появляется на реальной машине. Даже современные технологии пока не совершенны. Есть вращающиеся колеса, близость дорожного полотна и так далее. Пассажирский самолет, поверьте, спроектировать куда проще, чем современную машину Формулы 1...»
Перевел и адаптировал материал: Александр Гинько
Источник: http://f1i.com/magazine/328122-tech-f1i-a-visit-to-renault-at-enstone-the-design-office.html